UV Laser maker machine Sensitive Materials No Heat No Ink Ultra-Clean Finish
Detailed Diagram
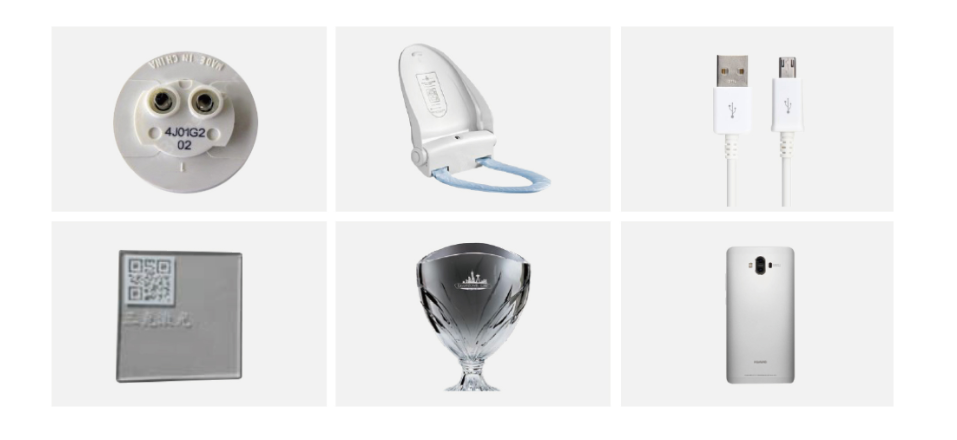
What Is a UV Laser Marking Machine?
A UV laser marking machine is an advanced laser solution designed for ultra-fine marking on heat-sensitive and precision materials. Utilizing a short-wavelength ultraviolet laser — most commonly at 355 nanometers — this cutting-edge system excels in high-definition marking without producing thermal stress, earning it the nickname “cold laser marker.”
Unlike traditional laser systems that rely on high heat to burn or melt materials, UV laser marking uses photochemical reactions to break molecular bonds. This ensures cleaner edges, higher contrast, and minimal surface disruption — a key advantage when working with intricate or sensitive components.
This technology is ideal for demanding sectors where precision and cleanliness are paramount, such as pharmaceutical packaging, circuit boards, glassware, high-end plastics, and even food and cosmetic labeling. From engraving micro QR codes on silicon wafers to marking barcodes on transparent bottles, the UV laser delivers unmatched accuracy and durability.
Whether you're a manufacturer in need of permanent traceability solutions or an innovator seeking to enhance your product branding, a UV laser marking machine provides the flexibility, speed, and micro-level finesse to meet your goals — all while maintaining the integrity of your material.
How Does a UV Laser Marking Machine Work
UV laser marking machines use a special type of laser that works differently from traditional lasers. Instead of using heat to burn or melt the material, UV lasers use a process called “cold light marking.” The laser produces a very short-wavelength beam (355 nanometers) that contains high-energy photons. When this beam hits the surface of a material, it breaks the chemical bonds on the surface through a photochemical reaction, rather than heating the material.
This cold marking method means that the UV laser can create marks that are extremely fine, clean, and detailed — without causing damage, deformation, or discoloration to surrounding areas. It’s especially useful for marking delicate items such as plastic packaging, medical tools, electronic chips, and even glass.
The laser beam is guided by fast-moving mirrors (galvanometers) and controlled by software that allows users to design and mark custom text, logos, barcodes, or patterns. Because the UV laser doesn’t rely on heat, it’s perfect for applications where precision and cleanliness are critical.
Specification of UV Laser Marking Machine Work
No. | Parameter | Specification |
---|---|---|
1 | Machine Model | UV-3WT |
2 | Laser Wavelength | 355nm |
3 | Laser Power | 3W / 20KHz |
4 | Repetition Rate | 10-200KHz |
5 | Marking Range | 100mm × 100mm |
6 | Line Width | ≤0.01mm |
7 | Marking Depth | ≤0.01mm |
8 | Minimum Character | 0.06mm |
9 | Marking Speed | ≤7000mm/s |
10 | Repeat Accuracy | ±0.02mm |
11 | Power Requirement | 220V/Single-phase/50Hz/10A |
12 | Total Power | 1KW |
Where UV Laser Marking Machines Shine
UV laser marking machines excel in environments where traditional marking methods fall short. Their ultra-fine beam and low thermal impact make them suitable for tasks that require maximum precision and clean, damage-free finishes. Some practical application scenarios include:
Transparent Plastic Bottles in Cosmetics: Imprinting expiration dates or batch codes on shampoo bottles, cream jars, or lotion containers without damaging the glossy surface.
Pharmaceutical Packaging: Creating tamper-proof, sterile markings on vials, blister packs, pill containers, and syringe barrels, ensuring traceability and regulatory compliance.
Micro QR Codes on Microchips: Etching high-density codes or ID marks on semiconductor chips and printed circuit boards, even in areas less than 1 mm² in size.
Glass Product Branding: Personalizing glass perfume bottles, wine glasses, or lab glassware with logos, serial numbers, or decorative elements without chipping or cracking.
Flexible Film & Foil Packaging: Non-contact marking on multilayer films used in food and snack packaging, with no ink or consumables required and no risk of material warping.
High-End Electronics: Permanent branding or compliance markings on smartphone housings, smartwatch components, and camera lenses made from sensitive polymer or ceramic composites.
About Us
XKH specializes in high-tech development, production, and sales of special optical glass and new crystal materials. Our products serve optical electronics, consumer electronics, and the military. We offer Sapphire optical components, mobile phone lens covers, Ceramics, LT, Silicon Carbide SIC, Quartz, and semiconductor crystal wafers. With skilled expertise and cutting-edge equipment, we excel in non-standard product processing, aiming to be a leading optoelectronic materials high-tech enterprise.
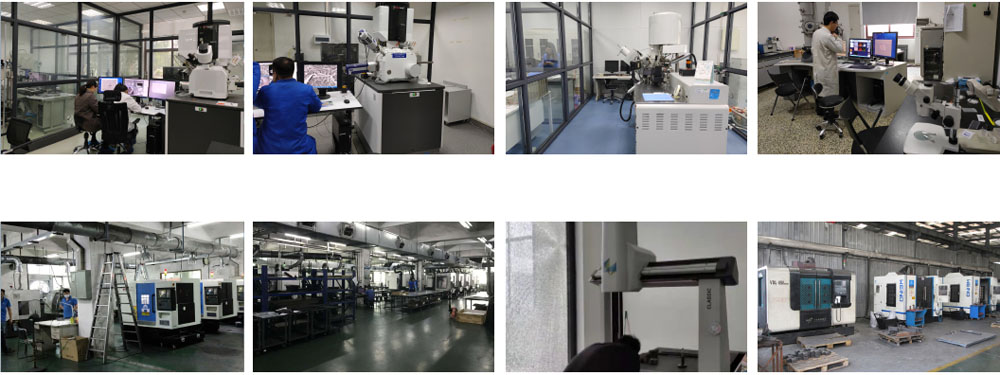
UV Laser Marking Machine – FAQ for Users
Q1: What is a UV laser marking machine used for?
A1: It’s used to mark or engrave text, logos, QR codes, and other designs on delicate items like plastic bottles, electronic parts, medical tools, and even glass. It’s especially useful when you need clear, permanent marks without heat damage.
Q2: Will it burn or damage the surface of my product?
A2: No. UV lasers are known for “cold marking,” which means they don’t use heat like traditional lasers. This makes them very safe for sensitive materials — there’s no burning, melting, or warping.
Q3: Is this machine difficult to operate?
A3: Not at all. Most UV laser machines come with easy-to-use software and preset templates. If you can use basic design software, you can operate a UV laser marker with just a bit of training.
Q4: Do I need to buy inks or other supplies?
A4: No. One of the best things about UV laser marking is that it’s contact-free and doesn’t require ink, toner, or chemicals. It’s eco-friendly and cost-effective over time.
Q5: How long will the machine last?
A5: The laser module usually lasts 20,000–30,000 hours depending on usage. With proper care and maintenance, the entire system can serve your business for many years.