Silicon Carbide Ceramic Fork Arm/Hand
Detailed Diagram
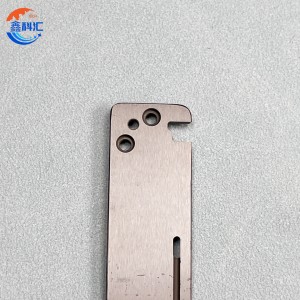
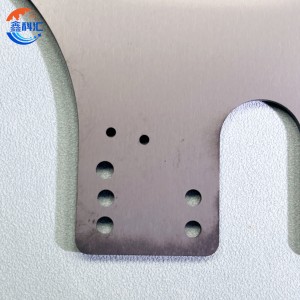
Introduce of Silicon Carbide Ceramic Fork Arm/Hand
The Silicon Carbide Ceramic Fork Arm/Hand is an advanced handling component developed for high-precision automation systems, particularly in semiconductor and optical industries. This component features a distinctive U-shape design optimized for wafer handling, ensuring both mechanical strength and dimensional accuracy under extreme environmental conditions. Crafted from high-purity silicon carbide ceramic, the fork arm/hand delivers exceptional rigidity, thermal stability, and chemical resistance.
As semiconductor devices evolve toward finer geometries and tighter tolerances, the demand for contamination-free and thermally stable components becomes critical. The Silicon Carbide Ceramic Fork Arm/Hand meets this challenge by offering low particle generation, ultra-smooth surfaces, and robust structural integrity. Whether in wafer transport, substrate positioning, or robotic tool heads, this component is engineered for reliability and longevity.
Key reasons to choose this Silicon Carbide Ceramic Fork Arm/Hand include:
-
Minimal thermal expansion for dimensional precision
-
High hardness for long service life
-
Resistance to acids, alkalis, and reactive gases
-
Compatibility with ISO Class 1 cleanroom environments

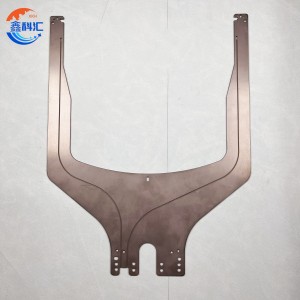
Manufacturing Principle of Silicon Carbide Ceramic Fork Arm/Hand
The Silicon Carbide Ceramic Fork Arm/Hand is produced through a highly controlled ceramic processing workflow designed to ensure superior material properties and dimensional consistency.
1. Powder Preparation
The process begins with the selection of ultra-fine silicon carbide powders. These powders are mixed with binders and sintering aids to facilitate compaction and densification. For this fork arm/hand, β-SiC or α-SiC powders are used to ensure both hardness and toughness.
2. Shaping and Preforming
Depending on the complexity of the fork arm/hand design, the part is shaped using isostatic pressing, injection molding, or slip casting. This allows for intricate geometries and thin-wall structures, crucial for the lightweight nature of the Silicon Carbide Ceramic Fork Arm/Hand.
3. High-Temperature Sintering
Sintering is performed at temperatures above 2000°C in vacuum or argon atmospheres. This stage transforms the green body into a fully densified ceramic component. The sintered fork arm/hand achieves near-theoretical density, providing outstanding mechanical and thermal properties.
4. Precision Machining
Post-sintering, the Silicon Carbide Ceramic Fork Arm/Hand undergoes diamond grinding and CNC machining. This ensures a flatness within ±0.01 mm and allows for the inclusion of mounting holes and locating features critical to its installation in automated systems.
5. Surface Finishing
Polishing reduces surface roughness (Ra < 0.02 μm), essential for reducing particulate generation. Optional CVD coatings can be applied to improve plasma resistance or add functionality such as anti-static behavior.
Throughout this process, quality control protocols are applied to guarantee the Silicon Carbide Ceramic Fork Arm/Hand performs reliably in the most sensitive applications.
Parameters of Silicon Carbide Ceramic Fork Arm/Hand
Main Specifications of CVD-SIC Coating | ||
SiC-CVD Properties | ||
Crystal Structure | FCC β phase | |
Density | g/cm ³ | 3.21 |
Hardness | Vickers hardness | 2500 |
Grain Size | μm | 2~10 |
Chemical Purity | % | 99.99995 |
Heat Capacity | J·kg-1 ·K-1 | 640 |
Sublimation Temperature | ℃ | 2700 |
Felexural Strength | MPa (RT 4-point) | 415 |
Young’ s Modulus | Gpa (4pt bend, 1300℃) | 430 |
Thermal Expansion (C.T.E) | 10-6K-1 | 4.5 |
Thermal conductivity | (W/mK) | 300 |
Applications of Silicon Carbide Ceramic Fork Arm/Hand
The Silicon Carbide Ceramic Fork Arm/Hand is widely used across industries where high purity, stability, and mechanical precision are essential. These include:
1. Semiconductor Manufacturing
In semiconductor fabrication, the Silicon Carbide Ceramic Fork Arm/Hand is used to transport silicon wafers within process tools such as etching chambers, deposition systems, and inspection equipment. Its thermal resistance and dimensional accuracy make it ideal for minimizing wafer misalignment and contamination.
2. Display Panel Production
In OLED and LCD display manufacturing, the fork arm/hand is applied in pick-and-place systems, where it handles fragile glass substrates. Its low mass and high stiffness enable fast and stable movement without vibration or deflection.
3. Optical and Photonic Systems
For alignment and positioning of lenses, mirrors, or photonic chips, the Silicon Carbide Ceramic Fork Arm/Hand offers vibration-free support, critical in laser processing and precision metrology applications.
4. Aerospace & Vacuum Systems
In aerospace optical systems and vacuum instruments, this component’s non-magnetic, corrosion-resistant structure ensures long-term stability. The fork arm/hand can also operate in ultra-high vacuum (UHV) without outgassing.
In all these fields, the Silicon Carbide Ceramic Fork Arm/Hand outperforms traditional metal or polymer alternatives in reliability, cleanliness, and service life.
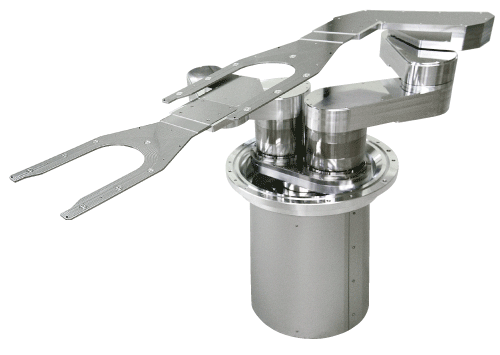
FAQ of Silicon Carbide Ceramic Fork Arm/Hand
Q1: What wafer sizes are supported by the Silicon Carbide Ceramic Fork Arm/Hand?
The fork arm/hand can be customized to support 150 mm, 200 mm, and 300 mm wafers. Fork span, arm width, and hole patterns can be tailored to fit your specific automation platform.
Q2: Is the Silicon Carbide Ceramic Fork Arm/Hand compatible with vacuum systems?
Yes. The fork arm/hand is suitable for both low-vacuum and ultra-high vacuum systems. It has low outgassing rates and does not release particulates, making it ideal for cleanroom and vacuum environments.
Q3: Can I add coatings or surface modifications to the fork arm/hand?
Certainly. The Silicon Carbide Ceramic Fork Arm/Hand can be coated with CVD-SiC, carbon, or oxide layers to enhance its plasma resistance, anti-static properties, or surface hardness.
Q4: How is the quality of the fork arm/hand verified?
Each Silicon Carbide Ceramic Fork Arm/Hand undergoes dimensional inspection using CMM and laser metrology tools. Surface quality is evaluated via SEM and non-contact profilometry to meet ISO and SEMI standards.
Q5: What is the lead time for custom fork arm/hand orders?
Lead time typically ranges from 3 to 5 weeks depending on complexity and quantity. Rapid prototyping is available for urgent requests.
These FAQs aim to help engineers and procurement teams understand the capabilities and options available when selecting a Silicon Carbide Ceramic Fork Arm/Hand.
About Us
XKH specializes in high-tech development, production, and sales of special optical glass and new crystal materials. Our products serve optical electronics, consumer electronics, and the military. We offer Sapphire optical components, mobile phone lens covers, Ceramics, LT, Silicon Carbide SIC, Quartz, and semiconductor crystal wafers. With skilled expertise and cutting-edge equipment, we excel in non-standard product processing, aiming to be a leading optoelectronic materials high-tech enterprise.
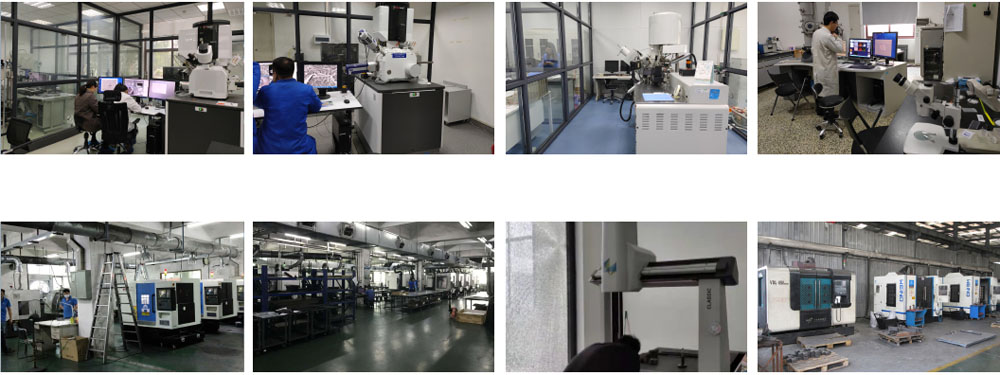