Infrared Picosecond Dual-Platform Laser Cutting equipment for Optical Glass/Quartz/Sapphire Processing
Main parameter
Laser Type | Infrared Picosecond |
Platform Size | 700×1200 (mm) |
900×1400 (mm) | |
Cutting Thickness | 0.03-80 (mm) |
Cutting Speed | 0-1000 (mm/s) |
Cutting Edge Breakage | <0.01 (mm) |
Note: Platform size can be customized. |
Key Features
1.Ultrafast Laser Technology:
· Picosecond-level short pulses (10⁻¹²s) combined with MOPA tuning technology achieve peak power density >10¹² W/cm².
· Infrared wavelength (1064nm) penetrates transparent materials through nonlinear absorption, preventing surface ablation.
· Proprietary multi-focus optical system generates four independent processing spots simultaneously.
2.Dual-Station Synchronization System:
· Granite-base dual linear motor stages (positioning accuracy: ±1μm).
· Station switching time <0.8s, enabling parallel "processing-loading/unloading" operations.
· Independent temperature control (23±0.5°C) per station ensures long-term machining stability.
3.Intelligent Process Control:
· Integrated material database (200+ glass parameters) for automatic parameter matching.
· Real-time plasma monitoring dynamically adjusts laser energy (adjustment resolution: 0.1mJ).
· Air curtain protection minimizes edge micro-cracks (<3μm).
In a typical application case involving 0.5mm-thick sapphire wafer dicing, the system achieves a cutting speed of 300mm/s with chipping dimensions <10μm, representing a 5x efficiency improvement over traditional methods.
Processing Advantages
1.Integrated dual-station cutting and splitting system for flexible operation;
2.High-speed machining of complex geometries enhances process conversion efficiency;
3.Taper-free cutting edges with minimal chipping (<50μm) and operator-safe handling;
4.Seamless transition between product specifications with intuitive operation;
5.Low operating costs, high yield rates, consumable-free and pollution-free process;
6.Zero generation of slag, waste liquids or wastewater with guaranteed surface integrity;
Sample display
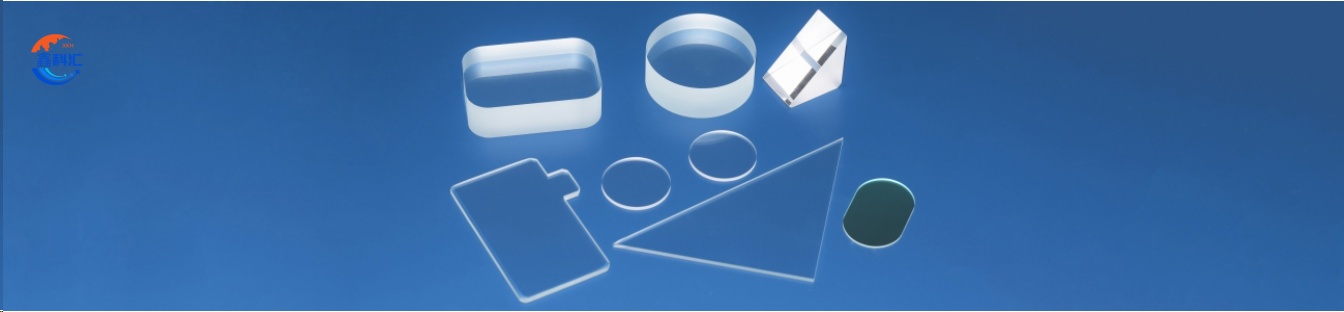
Typical Applications
1.Consumer Electronics Manufacturing:
· Precision contour cutting of smartphone 3D cover glass (R-angle accuracy: ±0.01mm).
· Micro-hole drilling in sapphire watch lenses (minimum aperture: Ø0.3mm).
· Finishing of optical glass transmissive zones for under-display cameras.
2.Optical Component Production:
· Microstructure machining for AR/VR lens arrays (feature size ≥20μm).
· Angled cutting of quartz prisms for laser collimators (angular tolerance: ±15").
· Profile shaping of infrared filters (cutting taper <0.5°).
3.Semiconductor Packaging:
· Glass through-via (TGV) processing at wafer level (aspect ratio 1:10).
· Microchannel etching on glass substrates for microfluidic chips (Ra <0.1μm).
· Frequency-tuning cuts for MEMS quartz resonators.
For automotive LiDAR optical window fabrication, the system enables contour cutting of 2mm-thick quartz glass with cut perpendicularity of 89.5±0.3°, meeting automotive-grade vibration test requirements.
Process Applications
Specifically engineered for precision cutting of brittle/hard materials including:
1.Standard glass & optical glasses (BK7, fused silica);
2. Quartz crystals & sapphire substrates;
3. Tempered glass & optical filters
4. Mirror substrates
Capable of both contour cutting and precision internal hole drilling (minimum Ø0.3mm)
Laser Cutting Principle
The laser generates ultrashort pulses with extremely high energy that interact with the workpiece within femtosecond-to-picosecond timescales. During propagation through the material, the beam disrupts its stress structure to form micron-scale filamentation holes. Optimized hole spacing generates controlled micro-cracks, which combine with cleaving technology to achieve precision separation.
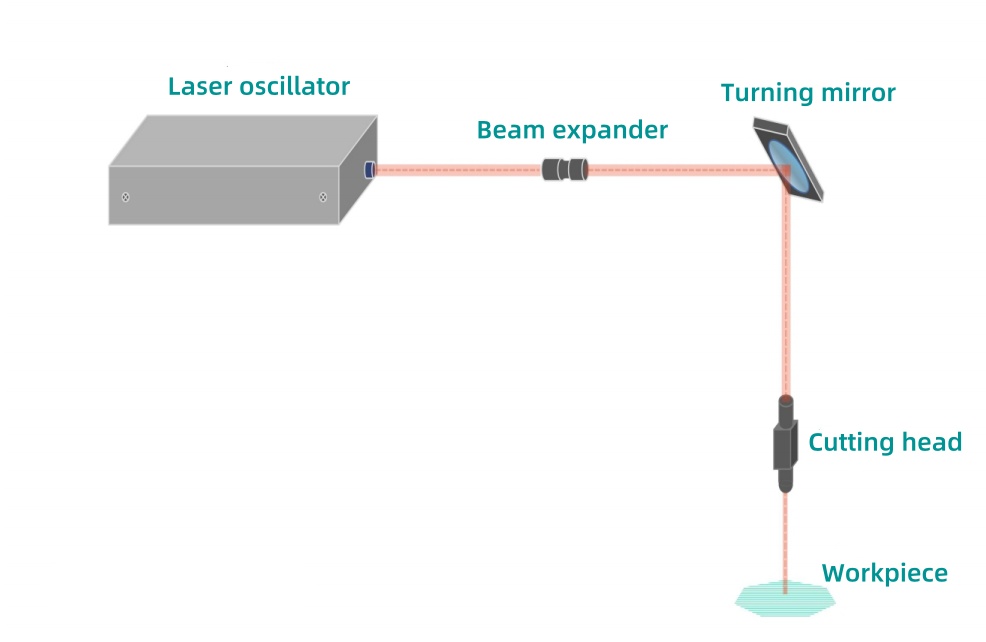
Laser Cutting Advantages
1.High automation integration (combined cutting/cleaving functionality) with low power consumption and simplified operation;
2.Non-contact processing enables unique capabilities unattainable through conventional methods;
3.Consumable-free operation reduces running costs and enhances environmental sustainability;
4.Superior precision with zero taper angle and elimination of secondary workpiece damage;
XKH provide comprehensive customization services for our laser cutting systems, including tailored platform configurations, specialized process parameter development, and application-specific solutions to meet unique production requirements across various industries.