Infrared Nanosecond Laser Drilling equipment for Glass Drilling thickness≤20mm
Main parameter
Laser type |
Infrared nanosecond |
Platform size |
800*600(mm) |
|
2000*1200(mm) |
Drilling thickness |
≤20(mm) |
Drilling speed |
0-5000(mm/s) |
Drilling edge breakage |
<0.5(mm) |
Note: Platform size can be customized. |
Laser Drilling Principle
The laser beam is focused at an optimal position relative to the workpiece thickness, then scans along predefined paths at high speed. Through interaction with the high-energy laser beam, target material is removed layer-by-layer to form cutting channels, achieving precise perforation (circular, square, or complex geometries) with controlled material separation.
Laser Drilling Advantages
· High automation integration with minimal power consumption and simplified operation;
· Non-contact processing enables unrestricted pattern geometries beyond conventional methods;
· Consumable-free operation reduces operational costs and enhances environmental sustainability;
· Superior precision with minimal edge chipping and elimination of secondary workpiece damage;
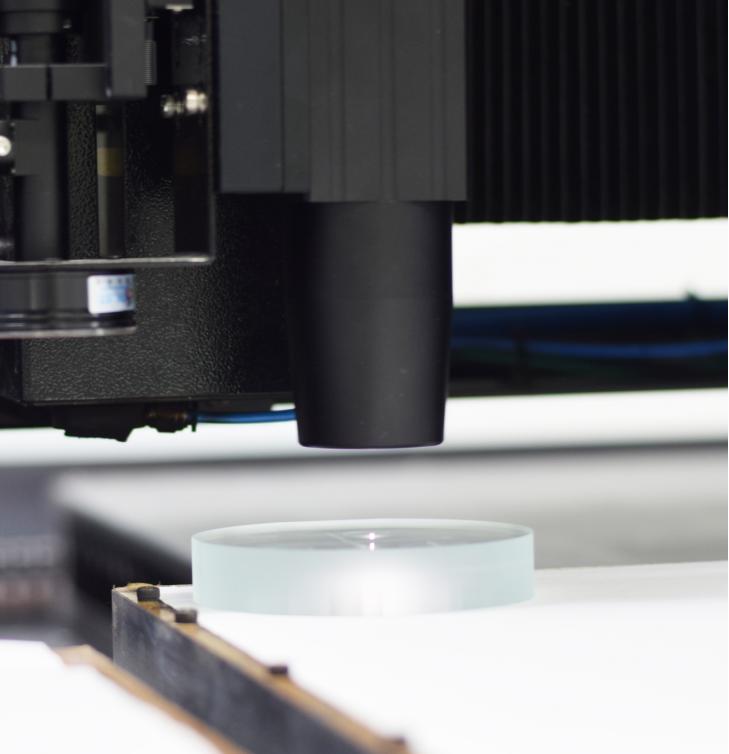
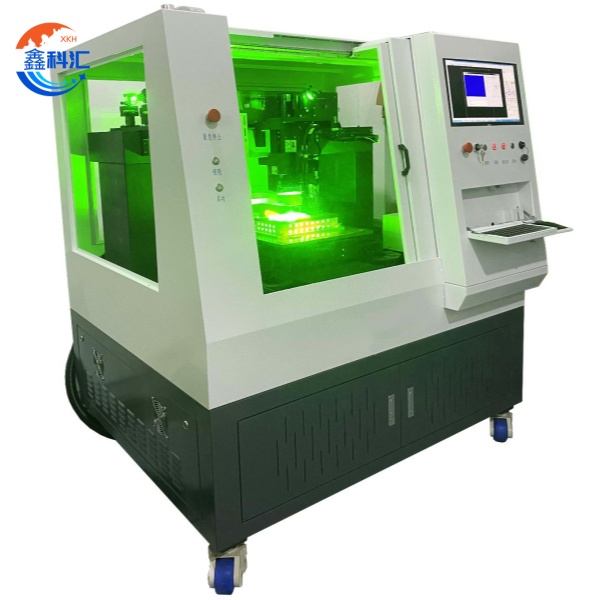
Sample display
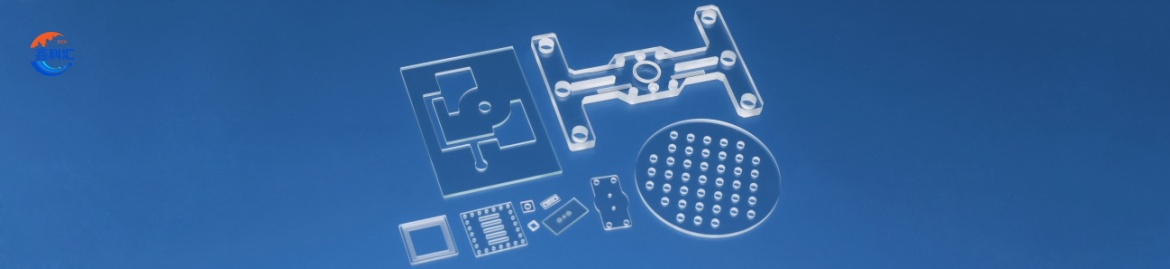
Process Applications
The system is engineered for precision processing of brittle/hard materials including drilling, grooving, film removal, and surface texturing. Typical applications include:
1. Drilling and notching for shower door components
2. Precision perforation of appliance glass panels
3. Solar panel via drilling
4. Switch/socket cover plate perforation
5. Mirror coating removal with drilling
6. Custom surface texturing and grooving for specialized products
Processing Advantages
1. Large-format platform accommodates diverse product dimensions across industries
2. Complex contour drilling achieved in single-pass operation
3. Minimal edge chipping with superior surface finish (Ra <0.8μm)
4. Seamless transition between product specifications with intuitive operation
5. Cost-efficient operation featuring:
· High yield rates (>99.2%)
· Consumable-free processing
· Zero pollutant emissions
6.Non-contact processing ensures surface integrity preservation
Key Features
1. Precision Thermal Management Technology:
· Utilizes a multi-pulse progressive drilling process with adjustable single-pulse energy (0.1–50 mJ)
· Innovative lateral air curtain protection system confines the heat-affected zone to within 10% of the hole diameter
· Real-time infrared temperature monitoring module automatically compensates energy parameters (±2% stability)
2. Intelligent Processing Platform:
· Equipped with a high-precision linear motor stage (repeat positioning accuracy: ±2 μm)
· Integrated vision alignment system (5-megapixel CCD, recognition accuracy: ±5 μm)
· Preloaded process database with optimized parameters for 50+ types of glass materials
3. High-Efficiency Production Design:
· Dual-station alternating operation mode with material changeover time ≤3 seconds
· Standard processing cycle of 1 hole/0.5 sec (Φ0.5 mm through-hole)
· Modular design enables rapid interchange of focusing lens assemblies (processing range: Φ0.1–10 mm)
Brittle Hard Material Processing Applications
Material Type | Application Scenario | Processing Content |
Soda-lime Glass | Shower doors | Mounting holes & drainage channels |
Appliance control panels | Drainage hole arrays | |
Tempered Glass | Oven viewing windows | Ventilation hole arrays |
Induction cooktops | Angled cooling channels | |
Borosilicate Glass | Solar panels | Mounting holes |
Laboratory glassware | Custom drainage channels | |
Glass-ceramic | Cooktop surfaces | Burner positioning holes |
Induction cookers | Sensor mounting hole arrays | |
Sapphire | Smart device covers | Ventilation holes |
Industrial viewports | Reinforced holes | |
Coated Glass | Bathroom mirrors | Mounting holes (coating removal + drilling) |
Curtain walls | Low-E glass concealed drainage holes | |
Ceramicized Glass | Switch/socket covers | Safety slots + wire holes |
Fire barriers | Emergency pressure relief holes |
XKH provides comprehensive technical support and value-added services for the infrared nanosecond laser glass drilling equipment to ensure optimal performance throughout the equipment lifecycle. We offer customized process development services where our engineering team collaborates closely with clients to establish material-specific parameter libraries, including specialized drilling programs for challenging materials like sapphire and tempered glass with thickness variations from 0.1mm to 20mm. For production optimization, we conduct on-site equipment calibration and performance validation tests, ensuring critical metrics such as hole diameter tolerance (±5μm) and edge quality (Ra<0.5μm) meet industry standards.