Silicon Dioxide wafer SiO2 wafer thick Polished, Prime And Test Grade
Introduce of wafer box
Product | Thermal Oxide (Si+SiO2) wafers |
Production Method | LPCVD |
Surface Polishing | SSP/DSP |
Diameter | 2inch / 3inch /4inch / 5inch/ 6inch |
Type | P type / N type |
Oxidation Layer thicnkess | 100nm ~1000nm |
Orientation | <100> <111> |
Electrical resistivity | 0.001-25000(Ω•cm) |
Application | Used for synchrotron radiation sample carrier, PVD/CVD coating as substrate, magnetron sputtering growth sample, XRD, SEM, Atomic force, infrared spectroscopy, fluorescence spectroscopy and other analysis test substrates, molecular beam epitaxial growth substrates, X-ray analysis of crystalline semiconductors |
Silicon oxide wafers are silicon dioxide films grown on the surface of silicon wafers by means of oxygen or water vapor at high temperatures (800°C~1150°C) using a thermal oxidation process with atmospheric pressure furnace tube equipment. The thickness of the process ranges from 50 nanometers to 2 microns, the process temperature is up to 1100 degrees Celsius, the growth method is divided into "wet oxygen" and "dry oxygen" two kinds. Thermal Oxide is a "grown" oxide layer, which has higher uniformity, better densification and higher dielectric strength than CVD deposited oxide layers, resulting in superior quality.
Dry Oxygen Oxidation
Silicon reacts with oxygen and the oxide layer is constantly moving towards the substrate layer. Dry oxidation needs to be performed at temperatures from 850 to 1200°C, with lower growth rates, and can be used for MOS insulated gate growth. Dry oxidation is preferred over wet oxidation when a high quality, ultra-thin silicon oxide layer is required. Dry oxidation capacity: 15nm~300nm.
2. Wet Oxidation
This method uses water vapor to form an oxide layer by entering the furnace tube under high temperature conditions. The densification of wet oxygen oxidation is slightly worse than dry oxygen oxidation, but compared to dry oxygen oxidation its advantage is that it has a higher growth rate, suitable for more than 500nm film growth. Wet oxidation capacity: 500nm~2µm.
AEMD's atmospheric pressure oxidation furnace tube is a Czech horizontal furnace tube, which is characterized by high process stability, good film uniformity and superior particle control. The silicon oxide furnace tube can process up to 50 wafers per tube, with excellent intra- and inter-wafers uniformity.
Detailed Diagram
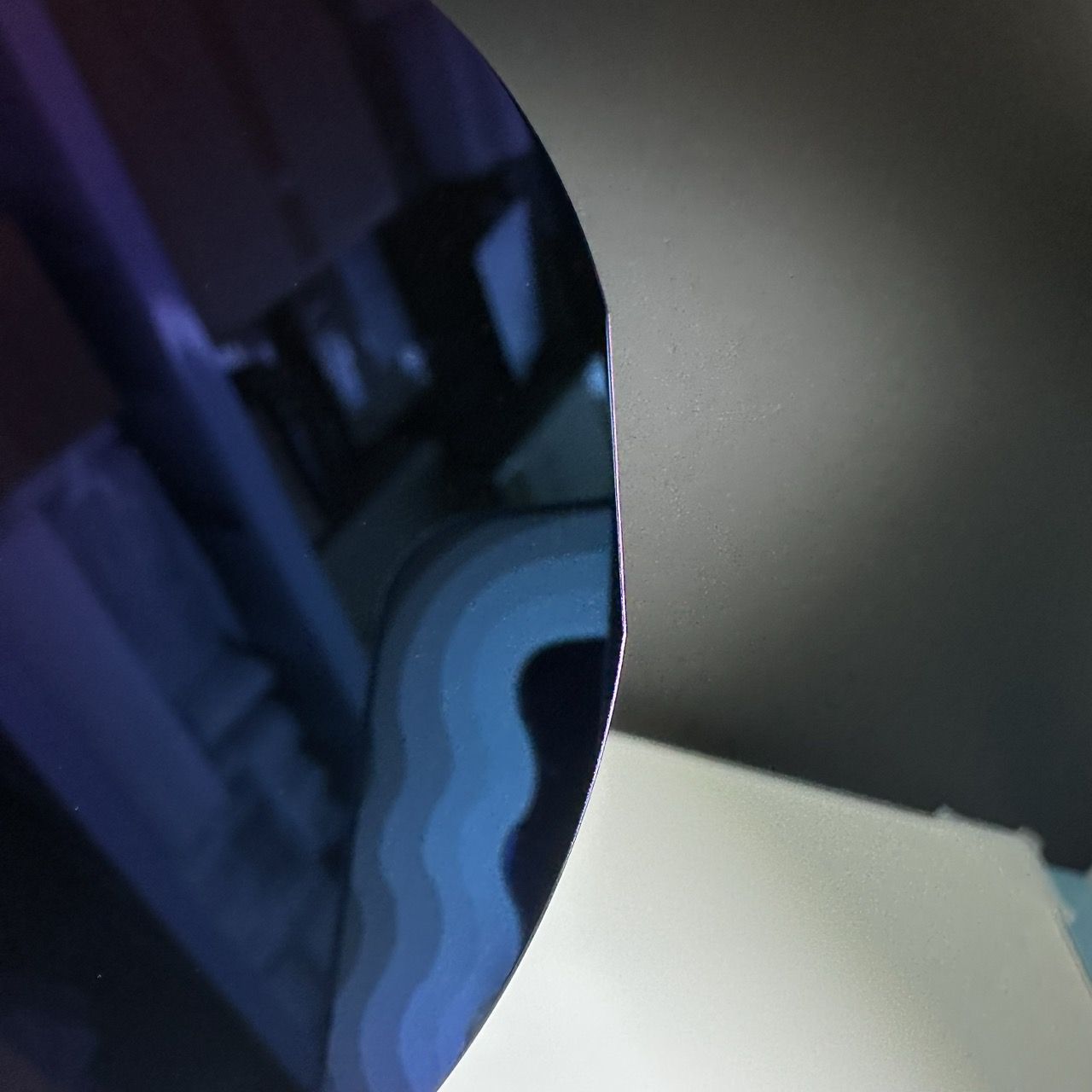
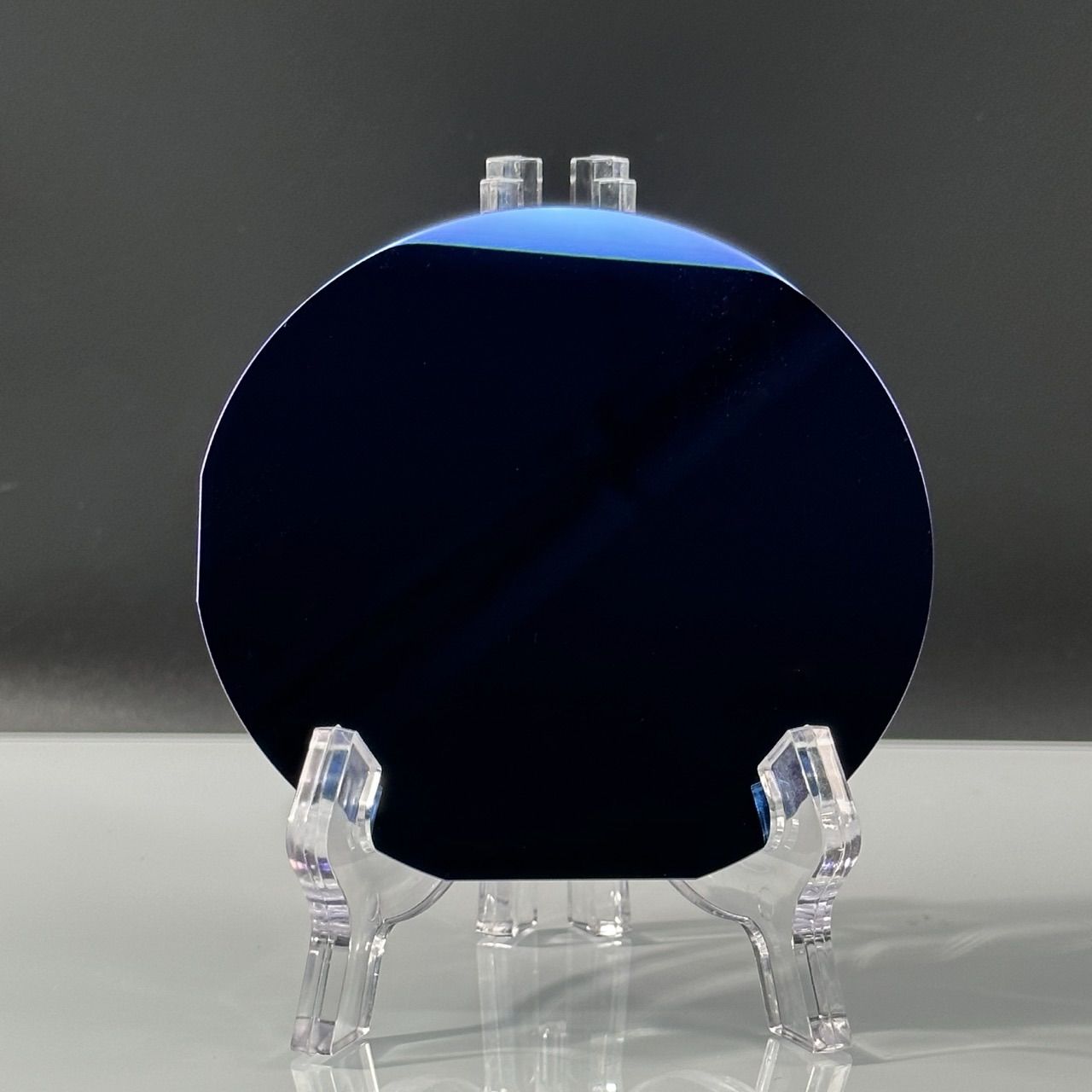